Gemechaniseerd DC Albert Heijn vraagt om accurate productdata
Over een jaar is het zover: dan is het eerste volledig gemechaniseerde distributiecentrum voor levensmiddelen in Nederland een feit. Albert Heijn is op dit moment druk met het testen en finetunen van het unieke opslag- en orderpicksysteem in Zaandam.
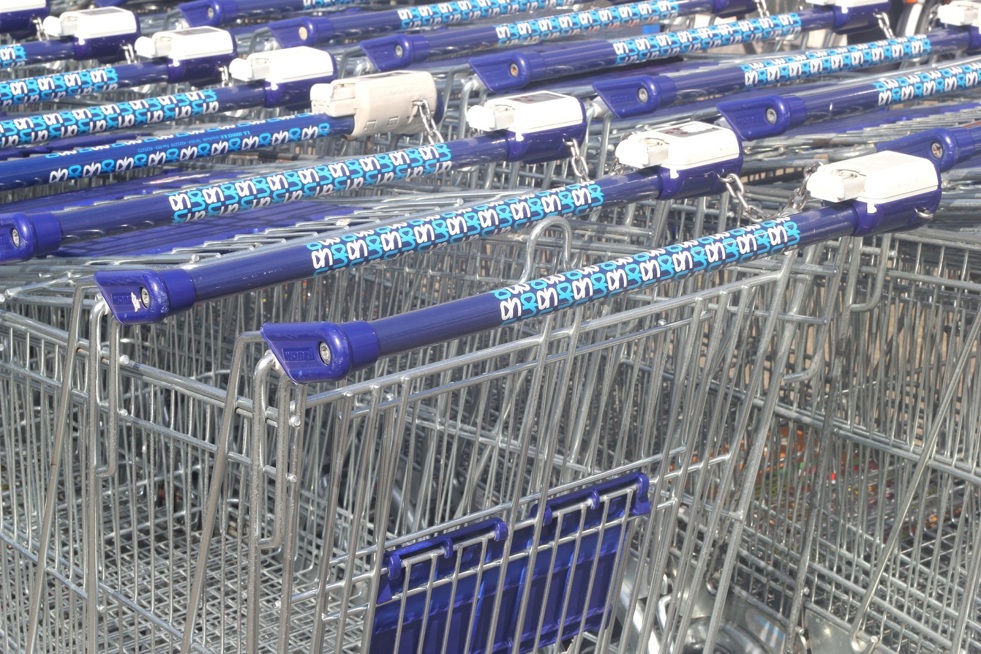
Het succes van de operatie is straks deels afhankelijk van de leveranciers. De kwaliteit van hun productdata in GS1 Data Source is cruciaal.
Albert Heijn is de eerste Nederlandse supermarktketen die een volledig gemechaniseerd distributiecentrum bouwt. Het pand is inmiddels gereed en alle machines zijn geïnstalleerd. De komende maanden staan in het teken van testen en finetunen. “Als alles volgens planning verloopt, nemen we het distributiecentrum vanaf het eerste kwartaal in 2019 stap voor stap in gebruik. Vanaf het eind van het tweede kwartaal moet het systeem volledig operationeel zijn. De overstap naar een gemechaniseerd distributiecentrum maakt het belang van goede palletlabels en productdata nog belangrijker”, vertelt René Baks, replenishment operations manager bij Albert Heijn.
Sneller inruimen van winkels
Het nieuwe distributiecentrum in Zaandam is één van de vier regionale distributiecentra van Albert Heijn. Als het straks operationeel is, zal het volledige proces van ontvangst tot opslag en orderpicking volledig gemechaniseerd zijn. Dat begint bij het ‘infeedstation’, waar elke pallet volledig automatisch wordt gecontroleerd. Pallets die deze controle doorstaan, worden vervolgens automatisch ontstapeld. De producten belanden op trays, die in stellingen worden gezet. Als er een order wordt opgestart, gaan de producten in de juiste volgorde naar de robot die ze op een rolcontainer stapelt.
“Een groot voordeel van mechanisatie is dat we de verdeling van producten over de rolcontainers kunnen afstemmen op de inrichting van elke winkel”, vertelt Baks. “In een manueel distributiecentrum zijn de mogelijkheden daartoe beperkt, omdat dat tot enorme loop- en rijafstanden zou leiden. In een gemechaniseerd distributiecentrum spelen die afstanden geen rol meer. Het resultaat is dat we tijd besparen bij het inruimen van winkels. Ander voordeel is dat we onze medewerkers kunnen ontlasten. Op drukke dagen moeten die nu veel tillen en lopen, dat is straks niet meer nodig.”
“Een groot voordeel van mechanisatie is dat we de verdeling van producten over de rolcontainers kunnen afstemmen op de inrichting van elke winkel”
Juiste plek voor labels
Voor een gestroomlijnd proces is het zaak dat het GS1 (pallet)label op de juiste plek is bevestigd, zodat die op het infeedstation probleemloos wordt gescand. “Natuurlijk moet het label zijn gekoppeld aan een elektronisch verzendbericht. Het liefst een verzendbericht waarin per pallet is aangegeven wat in welke volgorde op de pallet staat. Dat is informatie die ons systeem nodig heeft bij het afstapelen en opslaan van artikelen”, vertelt Baks.
Daarnaast moet het GS1 label goed leesbaar zijn en mag het niet over twee lagen zijn geplakt. “De meeste pallets zijn gewikkeld in folie, maar als dat niet het geval is krijgen we soms pallets met een label die over twee dozen is geplakt. Dat betekent dat die dozen aan elkaar blijven plakken, wat voor storingen bij het ontstapelen van pallets zorgt.”
Logistieke productdata luisteren nauw
Op colliniveau is het zaak dat de logistieke productdata zoals afmetingen en gewicht kloppen. “Die hebben we nodig om het meest efficiënte stapelpatroon van rolcontainers te kunnen berekenen, maar ook om de producten daadwerkelijk volgens dat stapelpatroon te kunnen stapelen. De toleranties luisteren nauw’, vertelt Baks.
Cruciaal is straks de rol van het infeedstation. Dat controleert of het gewicht en de afmetingen van een pallet passen binnen de toleranties die op basis van de vastgelegde productdata is berekend. Is dat niet het geval, dan moet de pallet helemaal worden gecontroleerd. “Als we een nieuw product ontvangen, krijgen we vooraf een seintje. Dan kunnen we het product nameten en het systeem inleren. Maar als de leverancier een nieuwe verpakking hanteert, is dat niet altijd bekend. Dat leidt dan soms tot problemen. Dat is bijvoorbeeld ook het geval bij producten in glas. De dikte van het glas kan variëren, zodat we de producten soms moeten nameten en de toleranties in het systeem aanpassen.”
Professionaliseringsslag
Albert Heijn is anderhalf jaar geleden gestart met het inlichten van de leveranciers over de mechanisatieplannen. Alle 160 leveranciers met producten die straks in het nieuwe systeem worden opgeslagen, zijn al rondgeleid. “Dat gaan we opnieuw doen nu het systeem draait. Bovendien hebben we al hun pallets inmiddels getest op één van de infeedstations. Onze bevindingen koppelen we direct aan hen terug.”
Baks benadrukt dat Albert Heijn niet opeens allemaal nieuwe eisen stelt aan labels en productdata. “Alleen luister het nu allemaal wat nauwer. Er zijn altijd redenen zoals storingen in de productie waarom pallets niet correct gelabeld zijn of waarom gegevens niet kloppen. In een manueel distributiecentrum kunnen we soms een oogje toeknijpen. Een infeedstation kan dat niet”, vertelt Baks, die spreekt van een professionaliseringsslag. “Dat is zoals de meeste leveranciers dat ervaren. Wat wij van leveranciers vragen, komt de hele sector ten goede. Zeker nu andere supermarktketens ook plannen voor gemechaniseerde distributiecentra hebben gepresenteerd.”