Hoogvliet ziet verstoringen in dc afnemen na maatregelen van Dr. Oetker
Het gemechaniseerde distributiecentrum van Hoogvliet draait drie jaar na de ingebruikname op volle toeren. Behalve op de momenten dat een zojuist geleverde pallet voor een verstoring in het systeem zorgt. Om de aanleverkwaliteit te verbeteren zoekt Hoogvliet de samenwerking met leveranciers. Zoals met Dr. Oetker, die op zoek is gegaan naar een andere wijze om pallets te stabiliseren.
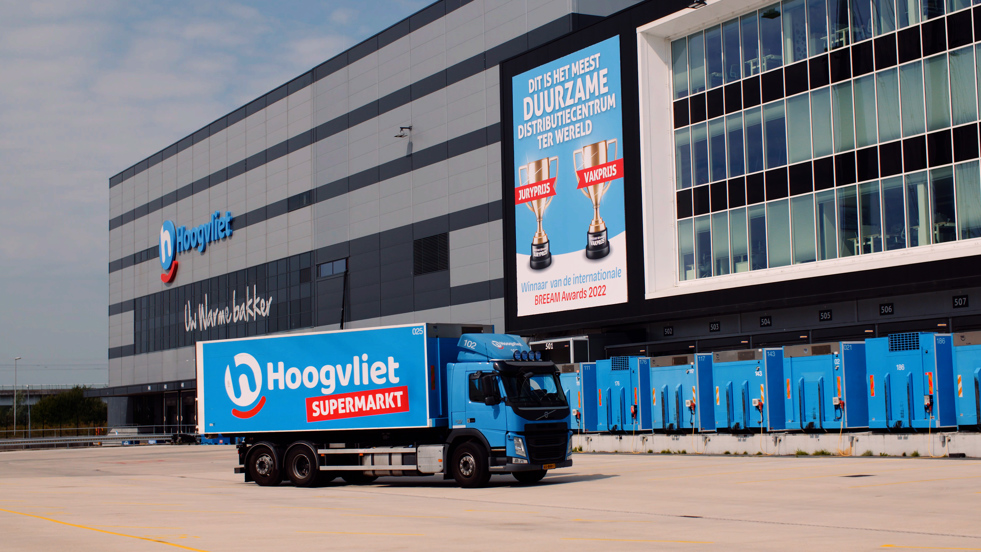
Dr. Oetker levert onder meer bakmixen, toetjes en diepvriespizza’s aan Hoogvliet. Tot voor kort was de foodproducent gewend om de omdozen van deze producten aan elkaar te plakken met hotmelt: een klein drupje lijm met net genoeg kleefkracht om de dozen niet van de pallet te laten vallen. “Door het gebruik van hotmelt hoefden we onze pallets niet te wikkelen in folie. Dat was belangrijk voor ons, want wij wilden graag zo min mogelijk verpakkingsafval de markt in brengen”, vertelt Marcel Rou, executive head of supply chain bij Dr. Oetker.
Voor de supermarktketens die de pallets van Dr. Oetker ontvingen, was het gebruik van hotmelt nooit een probleem. Als een orderpicker een doos pakte - eventueel na wat schudden - liet de lijm vanzelf los. “Maar voor de robots in het gemechaniseerde distributiecentrum van Hoogvliet is de kleefkracht net iets te groot”, stelt Rou. Dat wordt beaamd door John van Leijen, supply chain coördinator bij Hoogvliet. “Als de robot een laag met dozen van de pallet pakt, blijven de dozen daaronder soms hangen en valt het proces meteen stil. In dat geval moet er een medewerker aan te pas komen om de boel weer op gang te brengen. En afhankelijk van de verpakking kan het product zelfs stuk gaan.”
In een gemechaniseerd dc is sprake van een fabrieksmatig proces. Als het GS1 label niet op de juiste plek zit, kan de barcode niet door het systeem worden gescand en blijft de pallet op het dock staan.
Fabrieksmatig proces
Het hotmelt-voorbeeld laat zien tegen welke problemen supermarktketens met gemechaniseerde dc’s aanlopen. In een traditioneel dc gebeurt het werk door tientallen mensen die flexibel zijn. Als een doos blijft plakken, schudden ze eventjes. Als een GS1 label niet op de juiste plek zit, weten ze de barcode daarop toch te vinden. “Maar in een gemechaniseerd dc is sprake van een fabrieksmatig proces. Als het GS1 label niet op de juiste plek zit, kan de barcode niet door het systeem worden gescand en blijft de pallet op het dock staan. Als bij het afstapelen van pallets een storing optreedt, heeft dat direct gevolgen voor de processen voor en na de robot”, vertelt Jan van Rijn, supply chain manager bij Hoogvliet.
GS1 richtlijnen over de aanlevering van pallets
Drie jaar geleden was Hoogvliet de eerste supermarktketen in Nederland die een gemechaniseerd dc in gebruik nam voor zowel droge kruidenierswaren als voor versproducten. Ook Albert Heijn, Jumbo en Plus zijn dat pad ingeslagen. Om al die gemechaniseerde dc’s zo goed mogelijk te laten draaien, zijn in GS1 verband richtlijnen over de aanlevering van pallets opgesteld. Die geven onder andere aan dat de leverancier een GS1 verzend-bericht (DESADV) moet sturen en op de juiste plek een GS1 label moet plakken, zodat de pallet door de retailer automatisch kan worden ingeboekt. “Die richtlijnen helpen goed”, zegt Van Leijen. “Daarmee kunnen we een groot deel van de problemen afvangen. Maar er zijn ook zaken waarover we geen generieke afspraken kunnen maken. Dat heeft dan bijvoorbeeld te maken met het systeem zoals wij dat gebruiken.
Afspraken maken met leveranciers
Om verdere problemen te voorkomen, heeft Hoogvliet al voor de ingebruikname van het nieuwe dc een registratiesysteem opgezet. Als een pallet niet voldoet aan de aanleverspecificaties, leggen de dc-medewerkers dat vast, eventueel met foto’s om een en ander te verduidelijken. Eens per vier weken ontvangt de leverancier een rapportage met de bevindingen. Als een afwijking vaker voorkomt, gaat Hoogvliet met de leverancier in gesprek. “Het structureel delen van de afwijkingen doen we niet met alle leveranciers, want dat zijn er echt heel veel. Maar wel met de leveranciers die een hoge impact hebben op ons proces”, legt Van Leijen uit.
Dat klinkt als een arbeidsintensief proces. “Dat is het ook”, geeft Van Leijen toe. “Maar we merken dat alle aandacht helpt om de aanlevering van goederen te verbeteren. Ook nu, drie jaar na de ingebruikname, maken we nog regelmatig afspraken met leveranciers over een betere aanlevering van pallets.” Van Rijn vult aan: “Wij zijn ervan overtuigd dat we als Hoogvliet deze inspanning moeten leveren. Als het GS1 label op de verkeerde plek zit, is het aan ons om duidelijk te maken wat het probleem is. Dat kost tijd, maar die nemen we graag.”
We merken dat alle aandacht helpt om de aanlevering van goederen te verbeteren.
Met eigen ogen zien
Rou ervaart de samenwerking met Hoogvliet als uiterst constructief. De maandelijkse rapportage helpt om de aanlevering te verbeteren, evenals het bezoek aan het gemechaniseerde dc. “Vanuit het hoofdkantoor van Dr. Oetker is het gemakkelijk om te denken: wat een gezeur over een drupje lijm. Maar het helpt enorm om met eigen ogen het probleem te zien en de consequenties daarvan voor het proces van Hoogvliet.” Van Rijn neemt graag de tijd om leveranciers zoals Dr. Oetker te ontvangen: “We kunnen wel over hetzelfde praten, maar als we niet hetzelfde beeld erbij hebben, kunnen we elkaar toch verkeerd begrijpen. Daarom voegen wij foto’s toe aan de rapportages die wij versturen. Die geven heel veel inzicht. En inderdaad, soms helpt om met eigen ogen te zien wat het knelpunt is.”
Inmiddels heeft Dr. Oetker de hotmelt-machine in zijn fabriek uitgezet. Later dit jaar komt aan het eind van de productielijn een automatische foliewikkelmachine te staan. “Daarvoor moeten we dus een investering doen”, verklaart Rou. “Maar het stoppen met hotmelt is een eis van alle supermarktketens met gemechaniseerde dc’s. Die investering doen we dus graag. Bovendien hebben we ontdekt dat die druppels lijm op elke doos ook niet bevorderlijk zijn voor de recycling van alle karton. Natuurlijk produceren wij nu meer folie, maar daarvoor bestaat een goed inzamelsysteem.”
Fouten in masterdata
De aanschaf van de foliewikkelmachine is niet de enige aanpassing in het proces van Dr. Oetker. In het productieproces zijn maatregelen genomen om te voorkomen dat het GS1label onder de wikkelfolie belandt en dus niet gescand kan worden. “De maandelijkse rapportage helpt ook om fouten in de masterdata te herkennen, zoals het aantal dozen per palletlaag. Het is de bedoeling dat Hoogvliet producten per pallet of palletlaag bestelt omdat hun distributiecentrum daarop is ingericht. Maar soms zien we dat Hoogvliet 14 dozen bestelt, terwijl er 20 in een palletlaag gaan. Dan passen we meteen de minimale bestelhoeveelheid aan in de datapool van GS1 waarmee we dit soort data aanleveren aan retail.”
Samen de aanlevering verbeteren
Door maatregelen zoals die van Dr. Oetker heeft Hoogvliet de aanleverkwaliteit flink zien stijgen. Het aantal leveringen met een foutloze vooraanmelding met het GS1 verzendbericht schommelt rond de negentig procent. Het aantal pallets dat niet aan de aanleverspecificaties voldoet, is lastiger in percentages uit te drukken. “Dat schommelt nogal, maar is in ieder geval veel beter dan bij de start. En het kan altijd nog beter”, stelt Van Rijn, die leveranciers met vragen over het aanleverproces oproept om contact op te nemen. “Wij verstrekken graag rapportages over de aanleverkwaliteit, maar dat heeft weinig zin als we daarover geen gesprek voeren. Ook als leveranciers bezig zijn met productontwikkeling, denken wij graag mee over verbeteringen. Het verbeteren van de aanlevering is een gezamenlijke uitdaging.”